Introduction to Black Annealed Wire
Black annealed wire is a widely used type of steel wire that has undergone an annealing process to make it softer and more flexible. By heating the wire in an oxygen-free environment and then cooling it slowly, the internal structure of the steel changes, enhancing its ductility and corrosion resistance while reducing brittleness.
Black annealed wire is characterized by its black surface (resulting from the annealing process), uniform softness, excellent flexibility, and high tensile strength. Due to its advantageous properties, it is a versatile material across many industries, including construction, agriculture, handicrafts, packaging, and daily civil use.
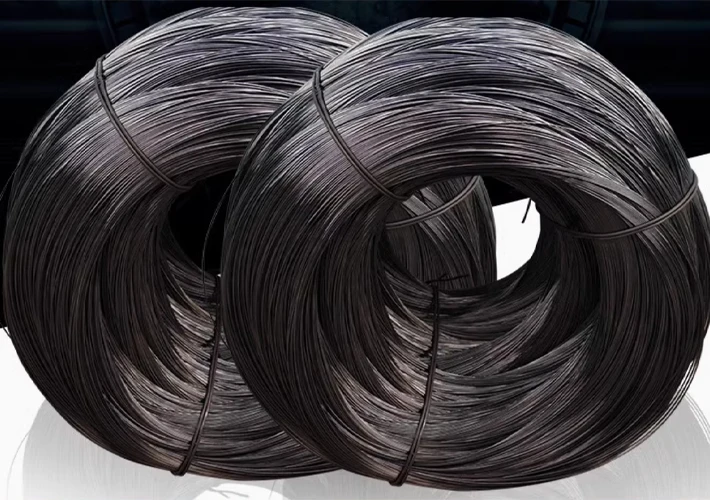
Specifications of Black Annealed Wire
When discussing the specifications of black annealed wire, several key parameters must be considered:
2.1 Material
Low Carbon Steel Wire: The most common material is Q195 or SAE 1008.
Chemical Composition (for Q195):
- Carbon (C): ≤0.12%
- Manganese (Mn): 0.30–0.60%
- Sulfur (S): ≤0.045%
- Phosphorus (P): ≤0.045%
Low carbon content ensures that the wire is soft and easy to process, while slight manganese improves its strength.
2.2 Diameter Range
Common diameter range: 0.15 mm to 5.0 mm
Popular diameters:
- 0.5mm, 0.7mm, 1.0mm, 1.2mm, 1.5mm, 2.0mm, 2.5mm
The choice of diameter depends on the specific application. Thinner wires are used for delicate binding, while thicker wires are used for heavier construction tasks.
2.3 Tensile Strength
- Typical tensile strength: 300–500 N/mm² (depending on wire size and customer requirements)
After annealing, the wire is soft yet retains enough strength for secure tying and binding purposes.
2.4 Coil Weight
- Small coil: 0.5 kg to 10 kg
- Big coil: 25 kg, 50 kg, or customized (up to 1000 kg for industrial uses)
2.5 Surface Treatment
- Oiled Surface: After annealing, a light oil layer is often applied to prevent oxidation and rust.
- Dry Surface: Some applications require oil-free wire for better cleanliness.
2.6 Packaging
- Inner Plastic Film: Protects the wire from moisture.
- Outer Hessian Cloth or Woven Bag: Protects against external damage.
- Pallet Packaging: For easier loading and unloading in export business.
- Custom Branding: Labeling and color-coding available upon request.
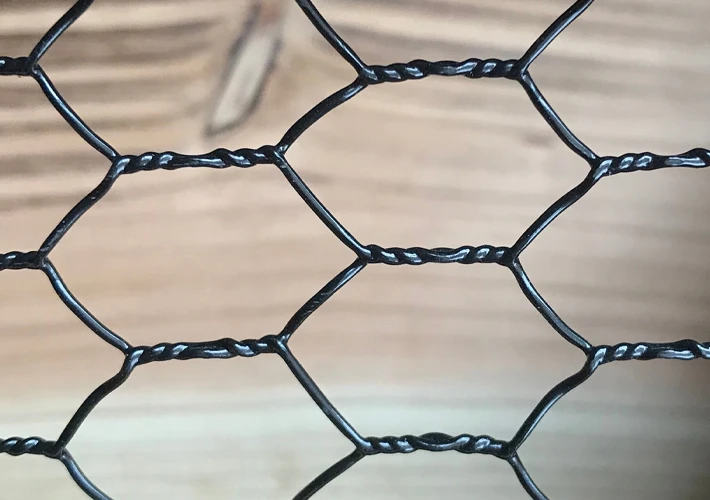
Production Process of Black Annealed Wire
Understanding the production process can help better appreciate the quality and versatility of black annealed wire:
Wire Rod Preparation: Select high-quality low-carbon steel rods.
Wire Drawing: Draw the rods through dies to reduce diameter.
Annealing: Heat treatment in a closed furnace at 600–700°C to soften the wire.
Surface Treatment: Cleaning, oiling, or dry finishing based on application.
Coiling and Packing: Coil the wire to specified weights, then pack for storage or shipment.
Key point: Proper annealing ensures uniform grain structure, resulting in consistent softness and flexibility.
Applications of Black Annealed Wire
Black annealed wire is extremely versatile. Its main applications include:
4.1 Construction Industry
- Binding Reinforcement Bars (Rebar Tying): Black annealed wire is used for tying rebars in concrete construction.
- Scaffolding Binding: Provides reliable securing for scaffolding elements.
- Wall Mesh and Frame Binding: Used in laying wall mesh before plastering.
Why: Its softness and ease of knotting make construction work faster and safer.
4.2 Agriculture
- Vineyard Support: Used for tying vines, tomatoes, and other climbing plants.
- Crop Binding: Helps in bundling hay or securing crops during transportation.
Why: The wire’s flexibility and smooth surface prevent damage to plants.
4.3 Packaging Industry
- Baling Wire: For securing bundles of recycled paper, cardboard, textiles, and plastic.
- Packaging Reinforcement: Used for heavy-duty packaging to ensure stability during transport.
Why: High flexibility combined with sufficient strength prevents slippage or breakage.
4.4 Handicrafts and DIY Projects
- Artworks: Sculptors and artists use black annealed wire for creating armatures and frames.
- Handmade Products: Used in creating custom baskets, lampshades, and decorative items.
Why: Easy shaping and manipulation encourage creativity.
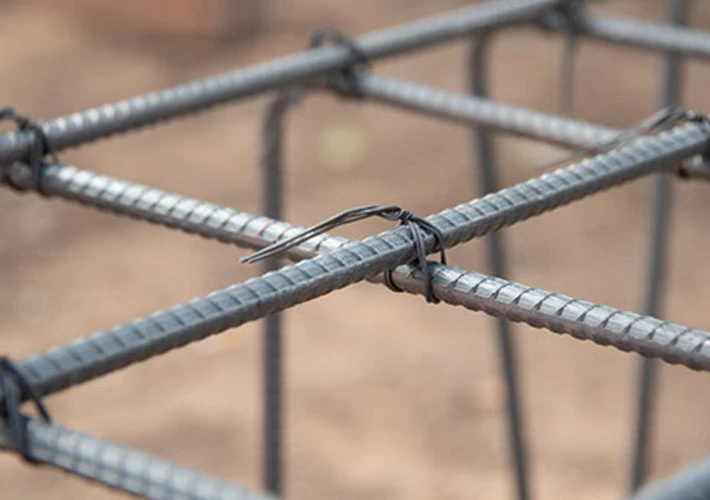
4.5 Fencing and Mesh Manufacturing
- Chain Link Fences: Used as raw material for manufacturing flexible wire meshes.
- Welded Wire Mesh: Black annealed wire is welded into mesh sheets for construction or fencing use.
Why: The wire’s ability to withstand welding temperatures makes it a preferred choice.
4.6 Household and Daily Applications
- General Tying: Securing items at home or on farms.
- Hooks and Hangers: Raw material for making basic household hooks and hangers.
Advantages of Black Annealed Wire
Understanding the benefits can help explain why black annealed wire is so popular:
Advantage | Explanation |
---|---|
Soft and Flexible | Easy to work with, does not require special tools for tying. |
Good Ductility | Can be bent and twisted without cracking. |
Economic Choice | Cost-effective for large-scale projects. |
Corrosion Resistance (with oiling) | Enhanced lifespan even in humid environments. |
Versatile | Suitable for multiple industries and applications. |
Customizable | Available in a wide range of diameters, coil sizes, and packaging. |
International Standards for Black Annealed Wire
Many countries have their own standards for black annealed wire:
- China: GB/T 343-2017
- USA: ASTM A853
- Europe: EN 10218-2
- Japan: JIS G 3532
These standards mainly govern wire diameter tolerances, tensile strength ranges, elongation, and surface quality. Compliance with these standards ensures that the wire meets the mechanical and chemical properties required by different markets.
Market Trends and Export Insights
As a key material in both developing and developed economies, the demand for black annealed wire remains stable.
Trends include:
- Increased demand for pre-oiled annealed wire to prevent rust.
- Custom-size coils for specific construction projects.
- Environmentally friendly annealing processes to reduce carbon emissions.
- Packaging innovations for easier international transportation.
Export Destinations:
- Southeast Asia (Vietnam, Indonesia, Thailand)
- Africa (Nigeria, South Africa, Egypt)
- Middle East (UAE, Saudi Arabia)
- South America (Brazil, Chile, Argentina)
- Europe (Poland, Germany, Spain)
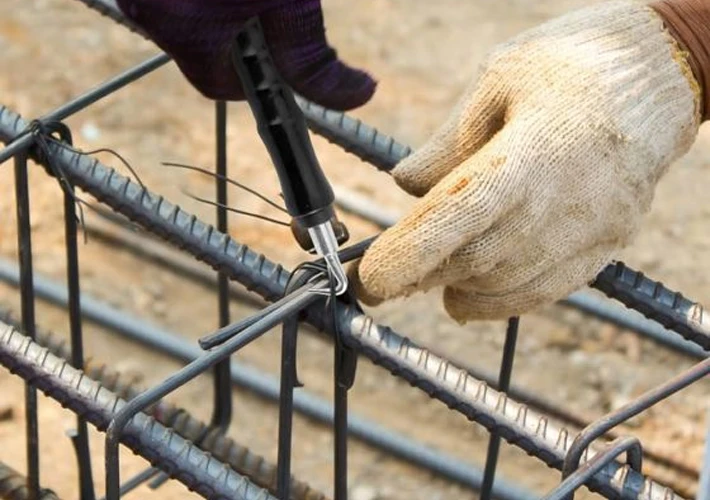
How to Choose High-Quality Black Annealed Wire
When purchasing black annealed wire, consider these factors:
- Material Certification: Confirm it is made from high-quality low-carbon steel.
- Tensile Strength Test Report: Ensure it meets your specific project requirements.
- Surface Inspection: Smooth surface, no rust, no cracks.
- Diameter Consistency: Stable diameter throughout the coil.
- Packaging Quality: Good packaging ensures no damage during transport.
Conclusion
Black annealed wire may appear to be a simple product, but it plays a vital role across countless industries worldwide. Its outstanding flexibility, strength, and adaptability to various environments make it indispensable. Whether in construction, agriculture, packaging, or artistic creations, black annealed wire provides an efficient and economical solution.
With the continuous advancement of production technology and environmental awareness, black annealed wire will evolve toward higher quality, more customization options, and eco-friendly production methods.
At LALAMETAL, we are committed to providing premium black annealed wire with consistent quality, competitive prices, and customized solutions to meet the diverse needs of global clients. With strict quality control, advanced production equipment, and rich export experience, LALAMETAL has become a trusted partner for customers worldwide.
Whether you are seeking reliable construction binding wire or high-performance packaging solutions, LALAMETAL is your ideal choice.
Feel free to contact us for more detailed specifications, samples, or custom requirements. We look forward to working with you and supporting your projects with the best quality products and services.