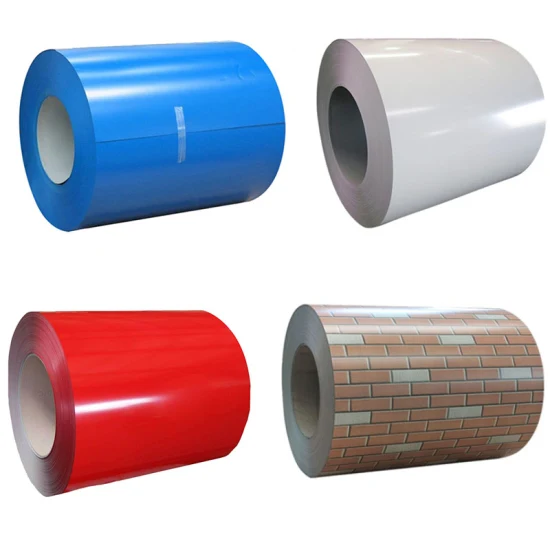
PPGL stands for Pre-Painted Galvalume sheets. Let’s break down the components of this term:
- Pre-Painted: This indicates that the sheets are coated with paint or a protective layer before being sold or used. The pre-painting process helps enhance the durability and appearance of the sheets.
- Galvalume: Galvalume is a type of steel product that is coated with a mixture of zinc and aluminum. This coating provides excellent corrosion resistance, making Galvalume sheets suitable for use in various environments, including those with high humidity or exposure to harsh weather conditions.
PPGL sheets are manufactured by first coating the Galvalume steel substrate with a primer to improve adhesion, followed by the application of a topcoat of paint. This process ensures that the sheets have both excellent corrosion resistance from the Galvalume coating and an attractive appearance from the paint layer.
PPGL sheets find applications in various industries, including construction, automotive, and appliances, where a combination of corrosion resistance and aesthetics is required. They are commonly used for roofing, siding, panels, and other architectural elements due to their durability, versatility, and ability to maintain their appearance over time.
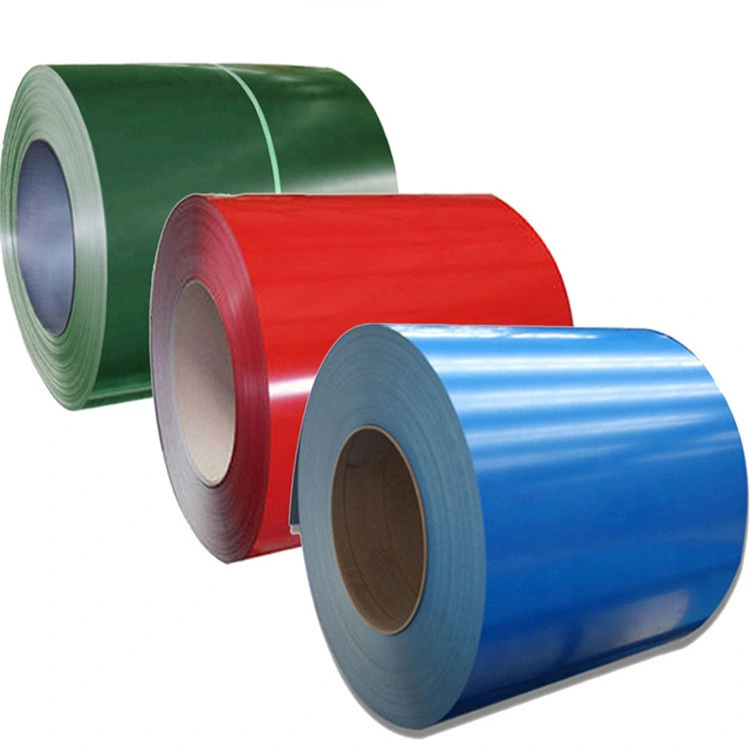
PPGI stands for Pre-Painted Galvanized Iron sheets. Here’s a breakdown of what this term means:
- Pre-Painted: Similar to PPGL sheets, PPGI sheets are coated with paint or a protective layer before being sold or used. This pre-painting process enhances the durability and aesthetics of the sheets.
- Galvanized Iron: PPGI sheets are made from galvanized iron, which is steel that has been coated with a layer of zinc to protect it from corrosion. The galvanization process involves immersing the steel in molten zinc or applying a zinc coating through other methods such as electroplating or hot-dip galvanizing. This zinc coating provides excellent corrosion resistance, making galvanized iron suitable for various applications in construction, manufacturing, and other industries.
PPGI sheets undergo a process where the galvanized iron substrate is first cleaned and treated to ensure proper adhesion, then coated with a primer to further enhance adhesion, and finally coated with a topcoat of paint. This process ensures that the sheets have both excellent corrosion resistance from the zinc coating and an attractive appearance from the paint layer.
PPGI sheets are commonly used for roofing, siding, panels, gutters, and other structural components in buildings and infrastructure projects. They offer a combination of strength, durability, corrosion resistance, and aesthetic appeal, making them a popular choice in construction applications.
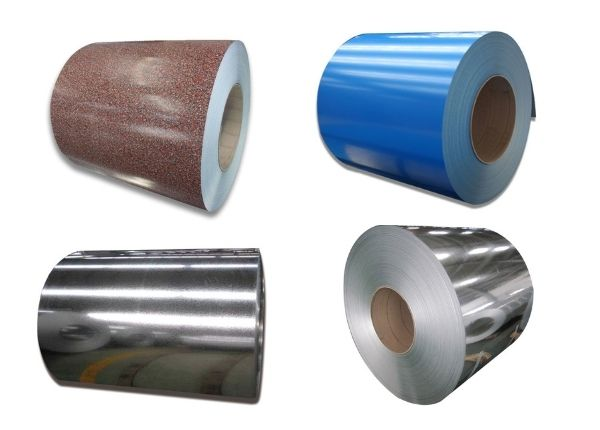
PPGI (Pre-Painted Galvanized Iron) and PPGL (Pre-Painted Galvalume) sheets are both widely used in construction and other industries, but they have some differences in terms of composition and properties:
1. **Base Material**:
– PPGI: PPGI sheets are made from galvanized iron, which is steel that has been coated with a layer of zinc to protect it from corrosion.
– PPGL: PPGL sheets are made from galvalume, which is a type of steel coated with a mixture of zinc and aluminum to provide enhanced corrosion resistance.
2. **Composition**:
– PPGI: The coating on PPGI sheets consists mainly of zinc, which provides protection against rust and corrosion.
– PPGL: The coating on PPGL sheets contains a mixture of zinc and aluminum, offering superior corrosion resistance compared to PPGI.
3. **Corrosion Resistance**:
– PPGI: While PPGI sheets offer good corrosion resistance due to the zinc coating, they may be more prone to corrosion in harsh environments compared to PPGL.
– PPGL: PPGL sheets provide better corrosion resistance, especially in environments with high humidity or exposure to chemicals, thanks to the aluminum content in the coating.
4. **Appearance**:
– PPGI: PPGI sheets typically have a shiny appearance due to the zinc coating.
– PPGL: PPGL sheets may have a slightly duller appearance compared to PPGI due to the presence of aluminum in the coating.
5. **Applications**:
– PPGI: PPGI sheets are commonly used in applications where corrosion resistance is not the primary concern, such as roofing, siding, and general construction.
– PPGL: PPGL sheets are preferred in applications where superior corrosion resistance is required, such as in coastal areas or industrial settings where exposure to corrosive elements is high.
6. **Cost**:
– PPGI: PPGI sheets are usually less expensive compared to PPGL sheets due to the difference in coating materials.
– PPGL: PPGL sheets tend to be slightly more expensive due to the higher cost of the aluminum-zinc coating.
Overall, while both PPGI and PPGL sheets offer protection against corrosion and are widely used in various applications, the choice between them depends on specific requirements such as the level of corrosion resistance needed, budget constraints, and aesthetic preferences.