Black annealed baling wire is made through a process that involves heating and cooling to improve its ductility, strength, and flexibility, making it ideal for various applications like baling, binding, and tying. Here’s a breakdown of the manufacturing process:
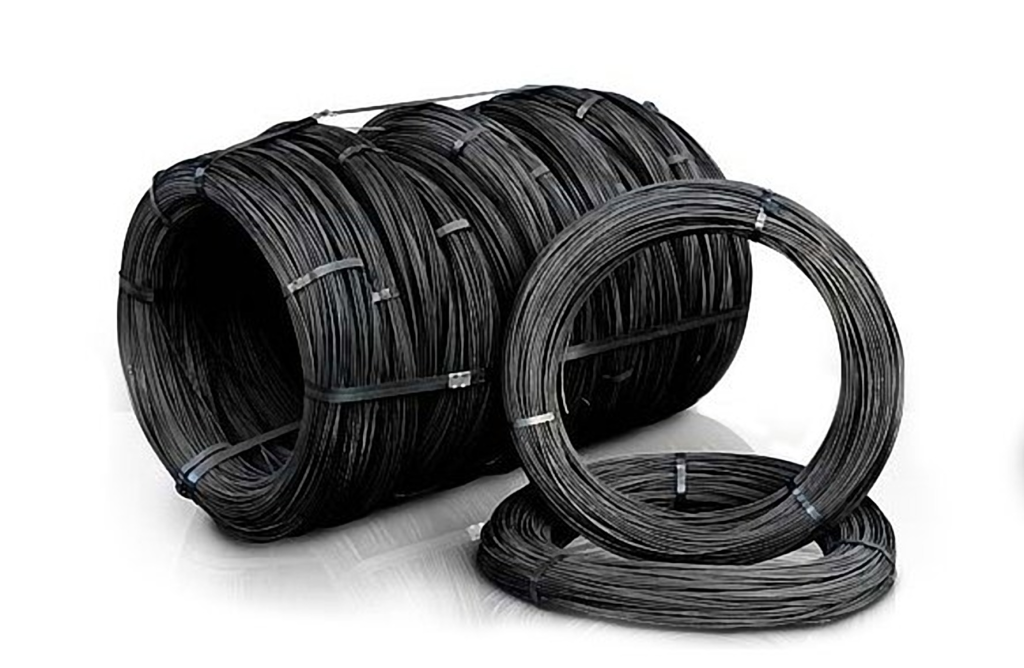
1. Wire Rod Production
- Raw Material Selection: The process starts with selecting a suitable low-carbon steel rod, typically with a carbon content ranging from 0.06% to 0.08%. The low carbon content is essential as it provides the desired balance between strength and flexibility.
- Hot Rolling: The steel rod is produced by hot rolling billets or blooms into a long, cylindrical shape. This rod is the base material for the wire drawing process.
2. Wire Drawing
- Initial Preparation: The steel rod is first cleaned to remove any scale, rust, or impurities. This cleaning is crucial to ensure a smooth surface and prevent any defects in the final wire.
- Lubrication: A lubricant, often a lime-based or soap solution, is applied to the rod to reduce friction during drawing and prevent the wire from breaking.
- Reduction in Diameter: The rod is pulled through a series of dies (a process called cold drawing) to reduce its diameter gradually. Each die is slightly smaller than the previous one, allowing the wire to be drawn thinner in multiple stages without breaking.
- Intermediate Annealing (Optional): Depending on the desired final thickness and properties, intermediate annealing may be done between drawing stages. This step involves heating the wire to relieve stress and restore ductility, making further drawing easier.
3. Annealing
- Full Annealing: After reaching the desired diameter, the wire undergoes full annealing. The wire is placed in an annealing furnace, where it is heated to temperatures typically ranging from 680°C to 750°C (1256°F to 1382°F).
- Controlled Atmosphere: The furnace atmosphere is carefully controlled, often using an inert or reducing atmosphere (like nitrogen, hydrogen, or a mixture of gases) to minimize oxidation on the wire’s surface.
- Soaking: The wire is held at the annealing temperature for a specific duration, allowing the microstructure of the steel to transform. This soaking period helps to reduce internal stresses, making the wire softer and more pliable.
- Cooling: Cooling is done in a controlled manner. Slow cooling inside the furnace is typical, allowing the wire to cool gradually to room temperature. This slow cooling process is essential to maintain the wire’s ductility and prevent it from becoming brittle.
4. Surface Treatment
- Pickling: The wire may undergo pickling, which involves immersing it in an acid bath to remove any remaining scale or oxides formed during the annealing process.
- Neutralizing: After pickling, the wire is rinsed and neutralized in an alkaline solution to remove any residual acid.
- Coating (Optional): To enhance corrosion resistance and improve handling, the wire may be coated with a thin layer of oil, phosphate, or another protective substance. This step is optional and depends on the specific application of the baling wire.
5. Finishing
- Straightening: The annealed wire may be passed through a straightening machine to ensure uniformity and ease of use in its final application.
- Cutting: The wire can be cut into specific lengths if it’s intended for tying or baling purposes. If not, it is wound into large coils or spools.
- Bundling: The cut wire or coils are then bundled, typically in 20 kg to 500 kg packs, depending on the customer’s requirements.
6. Quality Control
- Testing: The final product undergoes various quality checks, including tensile strength, elongation, and ductility tests, to ensure it meets the required standards.
- Inspection: The wire’s surface finish is inspected for uniformity, ensuring there are no defects like cracks or uneven coatings.
7. Packaging
- Coiling: The finished wire is wound into coils of varying sizes, usually in the range of 1 to 1000 kilograms.
- Strapping: The coils are secured with strapping material to maintain their shape and prevent unwinding during transport.
- Labeling: Each coil or bundle is labeled with important information, including wire gauge, weight, material grade, and other relevant details.
Properties of Black Annealed Wire
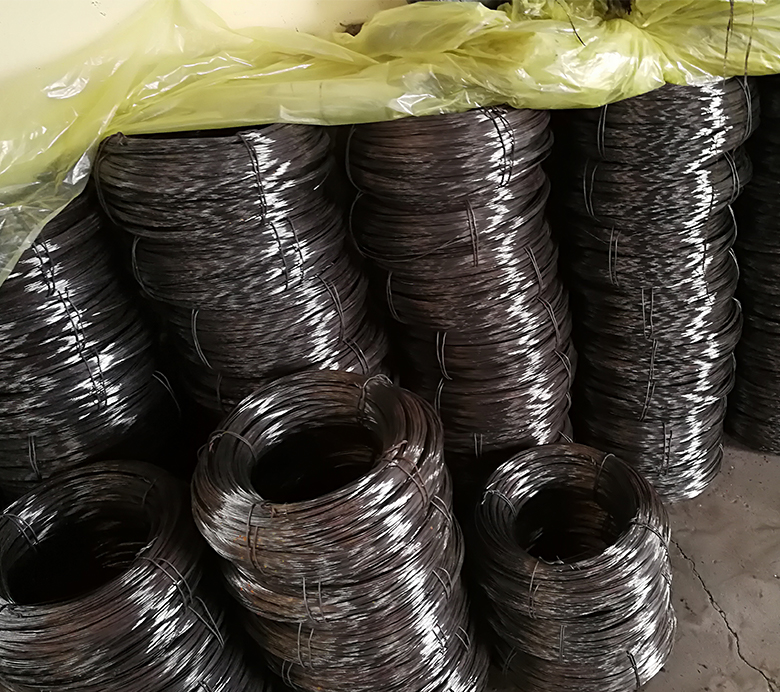
- Color: The wire has a characteristic black color due to the presence of iron oxide formed during the annealing process. This black finish is desirable for certain applications where a non-reflective surface is needed.
- Flexibility: The annealing process ensures that the wire is soft and flexible, making it ideal for tying, binding, and baling operations where ease of use is critical.
- Strength: Despite its flexibility, the wire retains sufficient tensile strength to hold together heavy loads, such as in baling hay, scrap metal, or recycling operations.
Applications
Black annealed wire is used in various industries, including agriculture, construction, and recycling. It is commonly used for:
- Baling Hay: Farmers use it to tie and secure bales of hay.
- Recycling: It is used to bundle recyclables, such as cardboard or metal, for transport.
- Construction: Builders use it to tie rebar in reinforced concrete construction.
- Packaging: It is used for tying and securing packages, particularly in industrial settings.
This comprehensive manufacturing process ensures that black annealed baling wire meets the required specifications for strength, flexibility, and durability, making it suitable for a wide range of industrial and agricultural applications.